Shipping and Receiving: Tips for Successful Warehouse Operations
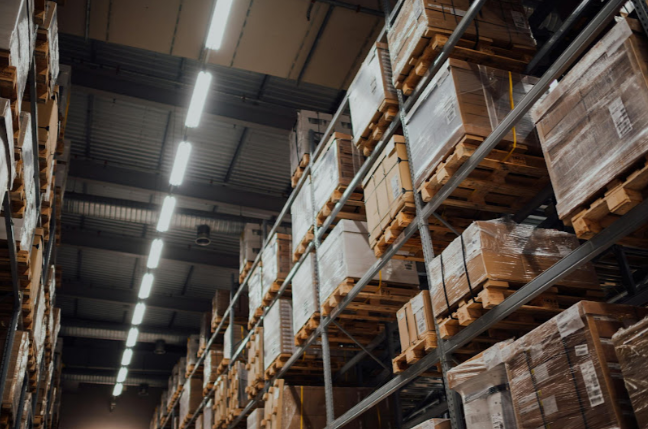
Efficient warehouse operations are the backbone of any successful distribution network. In today’s fast-paced market, shipping and receiving have become critical processes that determine how quickly products move from suppliers to customers. To maintain a competitive edge, businesses must optimize these processes for maximum efficiency. By honing the strategies for handling goods, companies can reduce delays, minimize errors, and improve overall customer satisfaction. Below, we will delve into key areas of warehouse operations and provide actionable tips to enhance your logistics.
Essential Tips for Streamlining Your Shipping Processes
Effective shipping starts with meticulous planning and organization. It’s vital to establish clear protocols for packing, labeling, and dispatching goods. This streamlines the shipping process and also ensures products reach customers in the best possible condition. Investing in quality packaging materials and training staff on proper packing techniques can significantly reduce the risk of damage during transit.
Time management plays a crucial role in shipping operations. Setting realistic timelines for each shipping stage, from picking orders to loading trucks, can help avoid bottlenecks. Additionally, scheduling regular maintenance checks for warehouse equipment like conveyors and forklifts ensures these tools are always ready to support peak performance in shipping tasks.
Digital tools can further refine the shipping process. Automated shipping software and enterprise resource planning (ERP) can assist in carrier selection, tracking shipments, and updating customers with real-time information. Embracing technology solutions provided by ERP vendors can be a game-changer. Using a powerful ERP system for optimizing your shipping strategy can provide you with better results.
Implementing an Effective Inventory Management System
An efficient inventory management system is essential to ensuring that products are available when customers place orders. Periodic audits and cycle counts should be part of your regular routine to maintain inventory accuracy. Discrepancies should be investigated promptly to avoid compounding errors that could lead to stock shortages or overages.
The use of inventory management software allows for better tracking and analysis of stock levels, turnover rates, and forecasting. These systems offer insights that can help in making informed decisions about reordering quantities and identifying slow-moving products that may require promotional efforts to move.
Demand forecasting is an integral part of inventory management. Understanding customer buying patterns and market trends can assist in making proactive decisions about stocking levels. This helps prevent overstocks that tie up capital and understocks that can lead to missed sales and customer dissatisfaction.
For continued education on the complexities of inventory management, professionals may consider enrolling in online MBA programs that specialize in supply chain management or operations. Such programs can provide deeper insights into strategies that align with business goals.
Enhancing Warehouse Layout for Improved Efficiency
The configuration of a warehouse has a direct impact on the speed and efficiency of operations. Optimizing the layout for the flow of goods can significantly reduce the time required for picking and packing orders. Positioning popular items near packing stations and ensuring clear pathways for forklifts and personnel are simple changes that can yield substantial benefits.
Storage solutions should be scalable to adapt to fluctuating inventory levels. Selective racking, for instance, may be preferable for a variety of stock-keeping units (SKUs), while denser storage solutions like drive-in racks can be suited for bulk items with less variation. Evaluating storage needs regularly ensures the warehouse layout remains conducive to current operations.
Zoning can be beneficial for storing similar items together or separating products based on size, weight, or handling requirements. This reduces the time spent searching for items and helps prevent errors during the picking process. Additionally, designated packing and staging areas ensure that there is a smooth transition from inventory to shipping.
Leveraging Technology for Accurate and Timely Order Fulfillment
Technology has become indispensable in modern warehouse operations. Implementing a warehouse management system (WMS) can lead to improved accuracy in order fulfillment by providing staff with detailed picking lists and optimized routes through the warehouse. This minimizes the time spent locating items and ensures orders are fulfilled accurately and on time.
Automation is playing an increasingly vital role in logistics. Robotics and conveyor systems can be integrated for repetitive tasks, such as moving goods from storage to shipping areas. This not only speeds up the process but also reduces the physical strain on workers, which can lead to increased productivity and lower injury rates.
Data analytics is also transformative, helping to identify patterns and inefficiencies in operations. Integrating data analytics with a WMS can anticipate bottlenecks, improve staffing decisions, and streamline workflow, all of which contribute to a more responsive and agile warehouse environment.
Altogether, the synchronization of shipping and receiving processes, along with a strategic focus on inventory management, warehouse layout, and technological innovation, offers a comprehensive approach to thriving in the competitive landscape of warehouse operations. By implementing the strategies discussed, businesses can achieve higher levels of efficiency, accuracy, and customer satisfaction.